Project Description
Desulfurization
Desulfurization
Ceramic enterprises in the production process mainly using coal gas as fuel, the flue gas containing SO2 and high concentration of dust and other substances, SO2 is the main material caused by acid rain, if directly discharged into the atmosphere, causing serious air pollution, affecting crop growth; and easy to produce Dust Haze phenomenon, is not conducive to the surrounding people’s health, affect the health of people living. In order to protect the environment and protect the people’s healthy life, it is necessary to invest a reasonable flue gas desulfurization equipment to treat the waste gas produced by the burning of the kiln.
Desulfurization technology
At present, there are three types of desulfurization methods: dry, semi dry and wet. Dry desulfurization, semi dry and wet desulfurization.Wet desulfurization efficiency of up to 98%. The characteristics of wet flue gas desulfurization technology is the end of the whole desulfurizationsystem in flue desulfurization process, desulfurization agent in solution, and the desulfurization product are wet desulfurization process, the reaction is a chemical reaction, the gas-liquid contact more fully, the sorbent utilization rate is high, the desulfurization efficiency is higher.
Flue gas desulfurization technology is mainly used absorbent or adsorbent to various alkaline trapping of sulfur dioxide in flue gas and
converted into a more stable and easy to mechanicalseparation ofsulfur compounds orsulfur,so asto achieve the purpose of desulfurization.
According to the types of desulfurizer, there are many methods such as Magnesium Oxide, lime, sodium hydroxide and sodium hydroxide.
|
Use material | Desulfurization principle | Advantage | Advantage | |
Lime method | calcium hydroxide | Calcium hydroxide reacts with S2O to form calcium sulfate precipitation | Limestone is cheaper | 1.Produce precipitates, easyto scale. 2. Desulfurization efficiencyis not high. |
|
Sodium alkali method | Sodium hydroxide | Sodium hydroxide reacts with S2O to form sodium sulfate, soluble | 1.High desulfurizationefficiency. 2.No fouling |
1. Alkali amount, high operating costs. 2. Alkaline strong, some corrosive |
|
Double alkali method | Sodium hydroxide/Calcium hydroxide | Sodium hydroxide reacts with S2O to form sodium sulfate, sodium sulfate reacts with calcium hydroxide to recover sodium hydroxide | 1. High desulfurization efficiency. 2. Calcium hydroxide does not enter the circulatory system, no scaling. 3. Renewable use of sodium hydroxide, alkali with less, low operating costs. |
Corrosive | |
Magnesium oxide method | Magnesium oxide | Magnesium oxide and water toproduce magnesium hydroxide,and then react with S2O to generatemagnesium sulfate, soluble | 1. High desulfurizationefficiency. 2. No fouling. 3. No corrosive. |
Compared to double-base operation costs are higher, lower than other methods. |
According to the advantages and disadvantages of desulfurization agent, our desulfurization equipment is selected double alkali method, which in principle the use of sodium alkali desulfurization to produce sodium sulfite and sodium sulfate, high desulfurization efficiency; calcium hydroxide does not enter the circulatory system, no scaling; The use of sodium hydroxide, alkali with less, low operating costs.
Double alkali introduction
For the absorption of sulfur dioxide in the flue gas, can be summarized as physical absorption and chemical absorption. Physical absorption refers to the mere absorption of sulfur dioxide by water, which is characterized by an increase in the amount of gas absorbed as the water temperature increases. The degree of physical absorption depends on the gas-liquid equilibrium as long as the partial pressure absorbed in the gas phase is greater than the partial pressure of the gas when the liquid phase equilibrates. The absorption process will proceed. As the physical absorption of the driving force is very small, lower absorption rate. Therefore, the water in the dust collector absorbs sulfur dioxide in the flue gas, and the absorption rate does not exceed 15%. And the chemical absorption has a very high absorption rate, the principle is: the absorption of sulfur dioxide gas and the absorption of NaOH chemical reaction, the sulfur dioxide gas and NaOH liquid components caused changes, effectively reducing the solution NaOH surface is absorbed sulfur dioxide gasOfthe partial pressure, increasing the absorption process of the driving force. Therefore, the chemical absorption rate of up to 95%.
Reaction equation
The main factor influencing the absorption of sulfur dioxide by alkali is the alkali concentration. After the study, sodium hydroxide absorption of sulfur dioxide, the concentration of lye on the chemical absorption of the mass transfer rate has a great impact. When the concentration of lye is low, the rate of chemical mass transfer is low. When the concentration of lye is increased, the mass transfer rate increases with the increase of alkali concentration. When the concentration of lye is increased to a certain value, the mass transfer rate reaches the maximum The At thistime the concentration of lye is called the critical concentration. When the lye concentration is higher than the critical concentration, the mass transfer rate does not increase. To this end, in the process of chemical absorption of flue gas desulfurization, when the use of alkali absorption of sulfur dioxide in the flue gas, the appropriate increase in lye concentration, can improve the absorption rate of sulfur dioxide. However, the concentration of lye can not exceed the critical concentration. When the critical concentration is exceeded, the desulfurization efficiency can not be improved. The optimum concentration of lye isthe critical concentration, at thistime, the desulfurization efficiency isthe
highest.
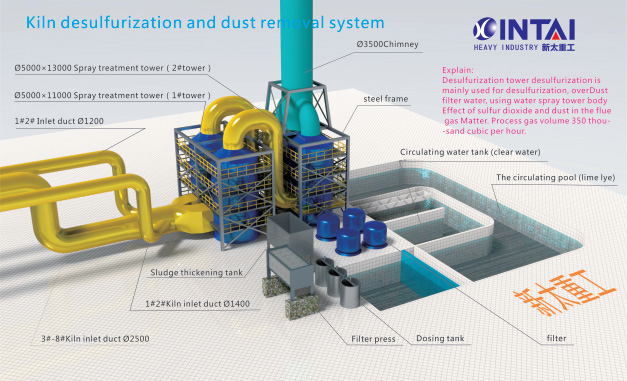
Double alkaline features
1. High desulfurization efficiency: sodium hydroxide activity, strong absorption capacity, do it with desulfurization agent does not producefouling substances, easy to operate.
2. The device is safe and reliable: the whole device is simple and practical structure, no pipe fouling failure.
3. The coal changes, load changes, desulfurization rate changes and other adaptability.
4. Running costs are low; the circulating liquid can be replaced by the lime water of the regeneration tank, can effectively save the amount of sodium hydroxide.